This new 29,000 sf Facilities Operations Center supports Los Angeles Mission College, one of nine campuses for the Los Angeles Community College District, and provides an exemplar of sustainability, functionality, and contextual response. Slated for construction in 2025, the two-building complex fits a tightly constrained site adjacent to the campus Central Plant, using modular dimensions and highly efficient circulation. The Facilities Maintenance and Operations Complex features extensive photovoltaic arrays and 10-hour battery storage to accommodate significant loads for equipment and vehicle charging. The system exceeds building and operational power needs by 40%. Embodied energy is mitigated using innovative concrete block with over 60% less production carbon than baseline concrete. A wide range of building product selections, as well as project-specific educational graphics, add to building performance to achieve targeted LEED Platinum.
A Model Complex for Campus Facilities and Operations
As the first Net Positive building in the District, the project is a step toward the District’s Integrated Energy Resource Plan, targeting carbon-free power by 2040. Its modest program of 8 shops, warehouse, offices, and support spaces belies its relatively high energy needs, given its dense array of powered equipment.
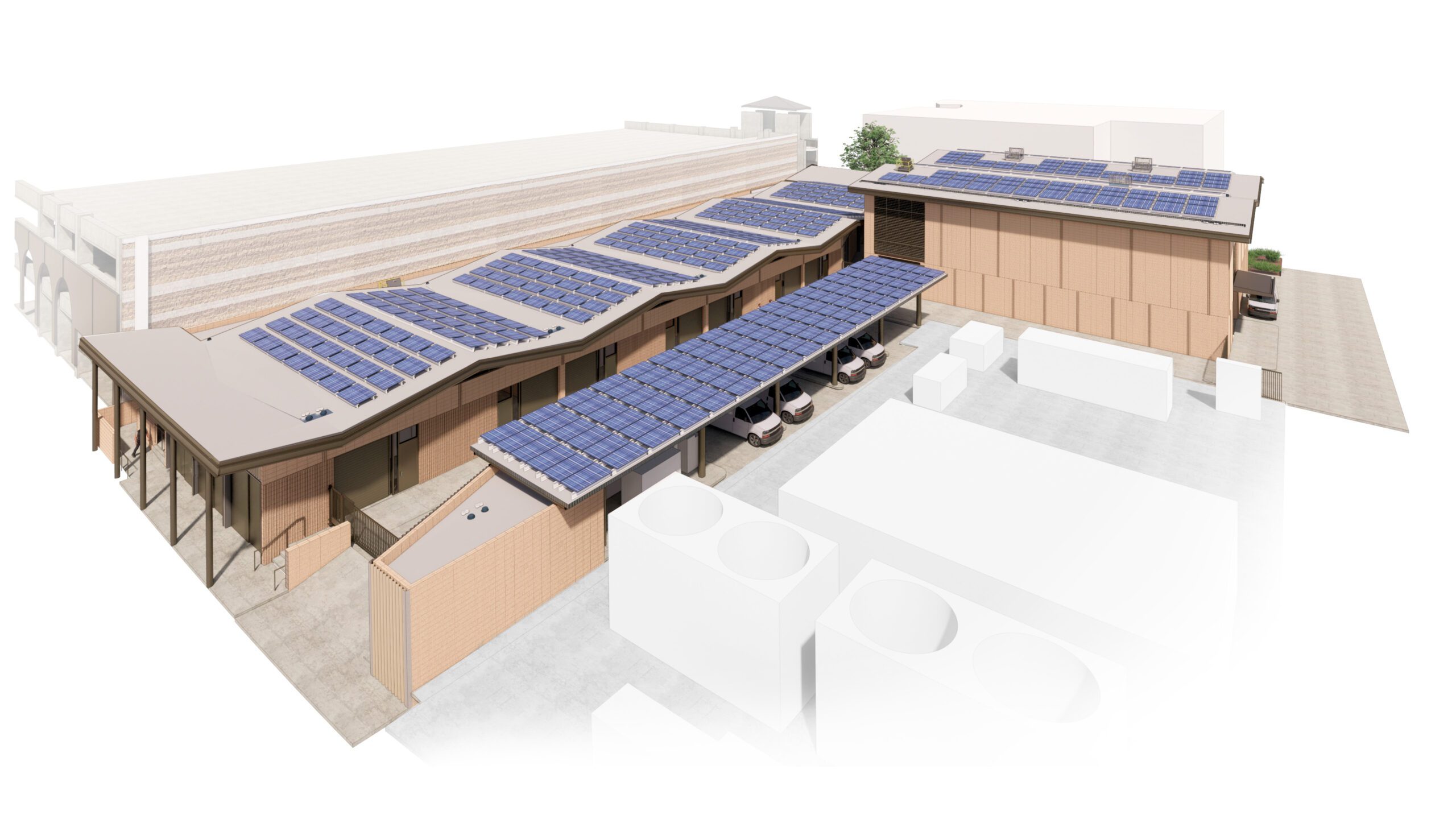
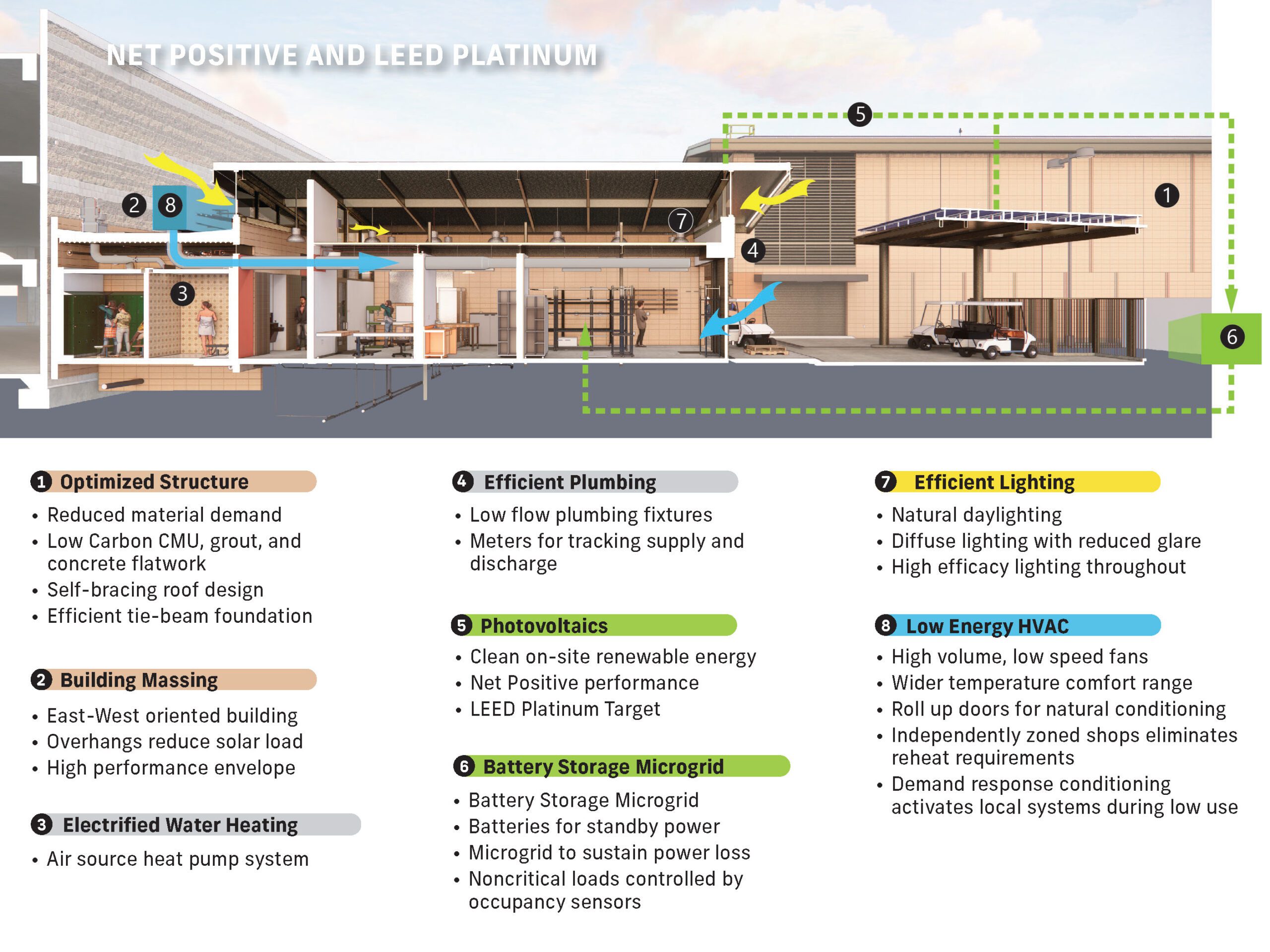
Design Excellence in a Function-driven Project
This design treats functionality and aesthetic quality as integral and inseparable. As a hard-working, process-driven building type, the design puts a high value on durability and upkeep, with simple, exposed structure and systems, creating a distinctive aesthetic that explains and celebrates the building fabric.
Site planning makes the most of a very tight buildable area by setting the shops building directly against the wall of the adjacent parking structure. This allowed a workable court space for vehicle parking and other support facilities, as well as a narrow gap between the shops and warehouse, critical as a passage for utility lines running to the campus from the central plant. A grand porch faces the campus interior, providing a shaded outdoor social setting for staff and visitors.
Modularity is a core principle — the shops and warehouse spaces were developed by testing the variety of fit-out and equipment for each type. The module is based on a rigorous pattern of concrete block walls carefully laid out to avoid cutting any blocks. The stacked block gave a ceiling height of 16 feet, from which the roof over each shop slopes up to 22 feet, allowing a shallow mezzanine for materials storage. Every shop has a generous garage door for service access and to allow indoor-outdoor workflow and fresh air.
Shops are accessed inside via a top-lit gallery lined with support spaces such as kitchenette and mechanical rooms. The flat roof over this bar conceals rooftop equipment.
The principal exterior material is the block, complemented by corrugated fiber cement panels and aluminum framed windows and doors. A 10-foot datum is established at the top of garage doors, highlighted by a change in the finish of the blockwork. For the double-height volume of the Warehouse, a rhythmic accent of fluted block breaks up the expansive surfaces. A base of terra cotta-colored units wraps and connects the entrance sides of both Warehouse and Shops.